PhD
phone : 04.83.16.66.13
mail : orquera@univ-tln.fr
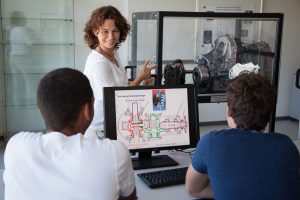
Bio
- Aggregation Professor in Industrial Engineering Sciences – Mechanical Engineering Option since 1999
- PhD defended in 2019
Research subject
Design for additive manufacturing: Downsizing of a mechanical system by multifunctional optimization
Thesis supervisor : Dominique MILLET, PR, University of Toulon, COSMER Lab
Co-supervisor : Sébastien CAMPOCASSO, Assoc. Prof, University of Toulon, COSMER lab.
Whatever the obtaining processes, the search for optimization has always been one of the main challenges in mechanical design. The arrival of the new additive manufacturing process (more commonly known as 3D printing) opens up new perspectives allowing, among other things, a gain in material, an improvement in part resistance and a reduction in the number of parts. In addition, the deposition of material layer by layer frees the user from the design constraints imposed by old manufacturing processes (such as machining, moulding, etc.). Thus it is possible to realize complex shapes, or even internal cavities.
To exploit all the opportunities of this process while respecting manufacturing constraints, we need new design rules and methodologies. This is why new design tools are being developed under the name “Design for Additive Manufacturing” (DfAM). However, most of the DfAM methods suggested in the literature remain focused on one part only. In addition, optimizations are mainly aimed at reducing the mass or number of parts, and more rarely at adding certain functions.
A new approach is being studied to achieve a multi-functional optimization of a kinematic assembly. This will lead to a methodology for downsizing on mechanisms in order, for example, to use less energy, reduce the space requirement, the mass, while obtaining at least the same output power. Then, to quantify the improvements and their added value, a new design indicator called “downsizing rate” will be defined.
Research Topic
Thanks to the freedom offered by additive manufacturing (AM) processes, design rules are evolving to lead to lighter and stiffer parts with really more complex shapes than those obtained by conventional processes. Worldwide, new tools of assistance to the design are developed, gathered under the naming “Design for Additive Manufacturing” (DfAM). However, most of the DfAM methods suggested in the literature remain focused on only one component and are not considering the product as a system of components. Moreover, optimizations are mainly limited on reducing the mass or the number of parts, and more rarely on adding some functions.
A new approach is presented to realize a multifunctional optimization of a mechanical system (MS). A methodology is first proposed in order to improve a product by using the AM opportunity. Then, to quantify the improvements of a system optimization, a new design indicator appointed “downsizing rate” is defined. Finally, a case study, applied to a compressed-air engine, is presented to demonstrate the relevance of the methodology and the downsizing rate. The design adapted to traditional manufacturing is compared to a part-by-part optimized design and a multifunctional optimized design, both adapted to additive manufacturing.
Education
- IUT GMP department of UTLN, SupMéca Toulon Engineering School, then SeaTech Engieneering School at UTLN
- Modules: CAD design, mechanical transmission, vibration, additive manufacturing, project management.